一、数据记录方法
(一)设备自带记录系统
多数冷热冲击试验箱配备内置数据记录装置。该装置能自动记录试验全程的关键数据,像温度变化曲线(涵盖升温、降温速率,高低温保持阶段的温度波动)、试验起始与结束时间、循环次数等。以某试验箱为例,其通过高精度温度传感器,每秒采集一次温度数据,并存储于设备内存,可存储长达一个月的试验数据。用户能在设备操作界面便捷查询过往试验数据,还可按日期、试验编号等条件筛选。 (二)外接数据采集设备
为获取更全面、精确的数据,常外接数据采集设备,如数据采集卡搭配专业数据采集软件。将多个高精度热电偶或温度传感器按特定布局安置在试验箱内,连接至数据采集卡。传感器将温度信号转化为电信号,数据采集卡以设定频率(如每秒 10 次)高速采集,再传输至电脑,由专业软件记录、存储。在航空航天零部件测试中,为精准掌握部件各部位在冷热冲击下的温度变化,在部件关键部位布置 10 个传感器,用外接数据采集设备记录,生成详尽温度变化图谱。
(三)人工记录辅助
在一些对特定现象需详细记录的试验里,人工记录作为辅助手段。操作人员在试验期间定时观察并记录样品外观变化,如是否出现裂纹、变形、变色,电子产品性能有无异常(如短路、断路、信号传输故障)等。在新材料研发测试时,人工每 30 分钟记录一次样品外观,结合设备自动记录的温度数据,综合分析材料性能变化。
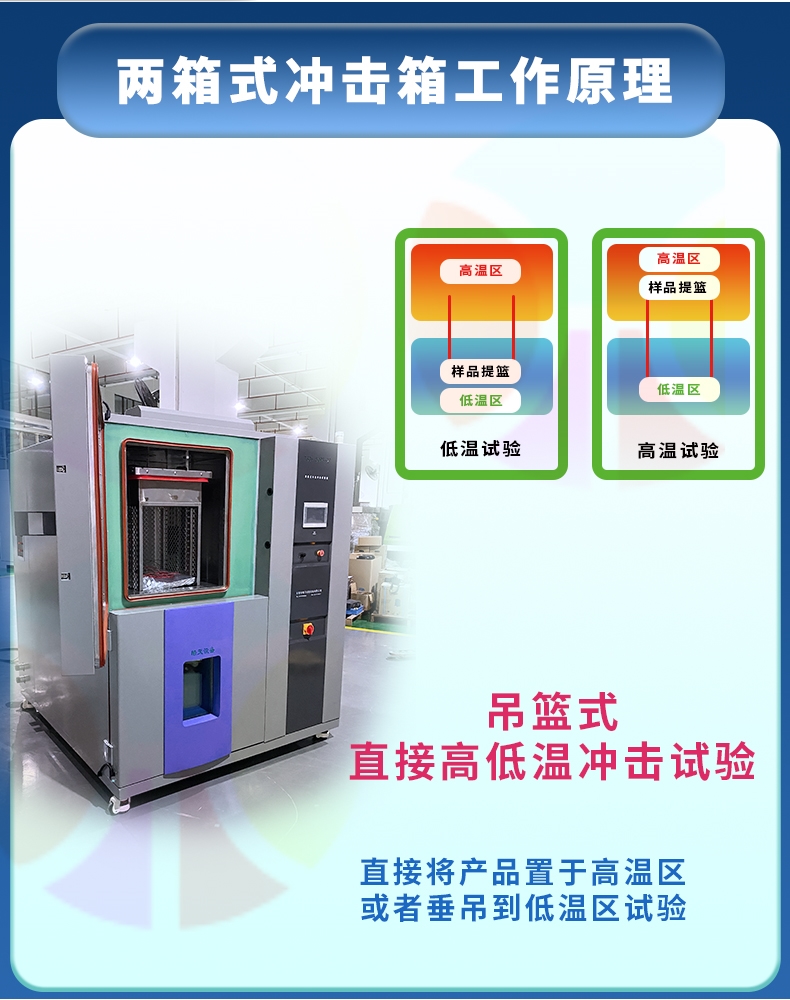
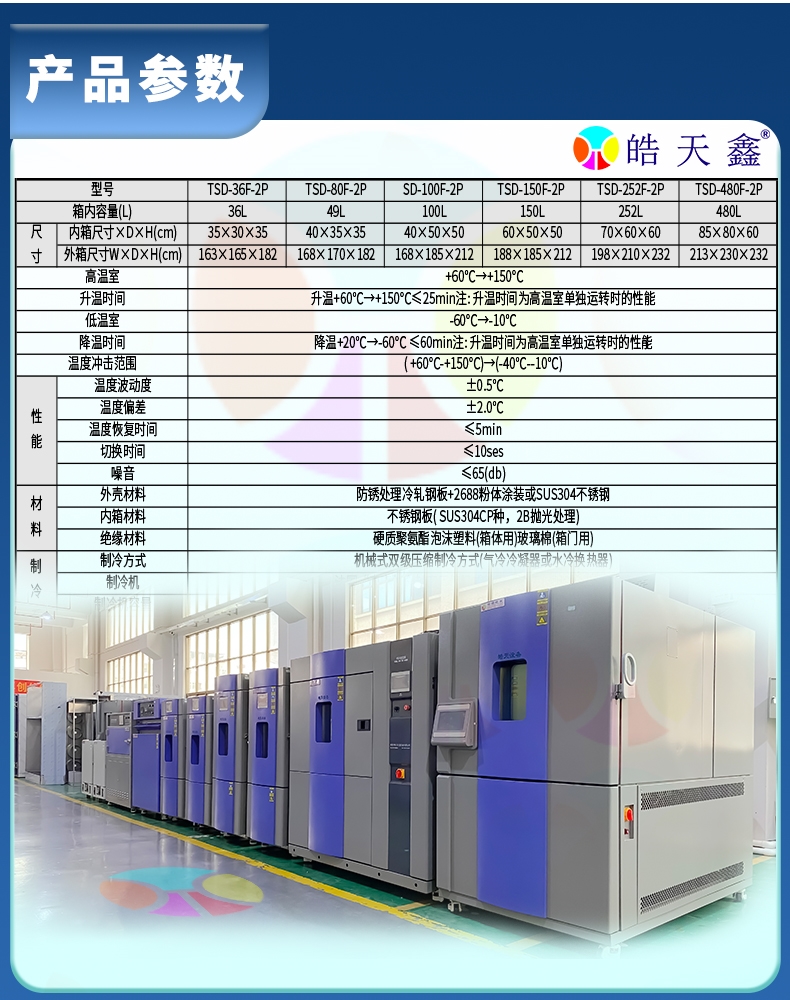

二、数据分析方法
(一)趋势分析
通过绘制温度 - 时间曲线,分析产品在整个试验过程中的温度响应趋势。从曲线能直观看出产品升温、降温是否顺畅,各阶段温度保持是否稳定。若在某循环中,升温时间明显延长,可能暗示试验箱加热系统有问题;产品在高温保持阶段温度波动超出允许范围,会影响产品性能评估准确性,需排查原因,如传感器故障、加热丝老化。
(二)对比分析
将试验数据与产品设计标准、过往试验数据对比。把新产品测试数据与设计要求的温度范围、循环次数下的性能指标对比,判断产品是否达标。也可对比同一产品不同批次试验数据,监控产品质量稳定性。若某批次产品在冷热冲击后性能下降幅度比之前批次大很多,要深入排查生产环节差异,如原材料质量波动、工艺参数改变。
(三)失效分析
针对试验中出现性能失效的产品,结合数据进行失效分析。依据记录的温度变化、样品外观及性能数据,确定失效是由高温、低温还是温度冲击引起,定位失效部件或材料。在电子产品测试中,若试验后某芯片功能异常,通过分析数据发现芯片所在区域在低温冲击时温度超设计下限,可能是低温导致芯片内部电路损坏,为产品改进提供方向,如优化芯片散热设计、选用更耐低温材料。